We are Manufacturer, Supplier, Exporter of Concrete PAN Mixer 400 from Satara, Maharashtra, India.
Every concrete product manufacturer has a fundamental requirement: To achieve the perfect concrete mix with the desired properties in the shortest possible time and at a reliable machine cost, Balaji PAN Type mixer is the most reliable solution to meet this requirement.
Balaji offers a wide range of concrete PAN Type mixers, ranging from 200 liters to 1000 liters concrete per batch. These mixers are designed to deliver the ideal concrete mix, resulting in improved productivity and efficiency for manufacturers.
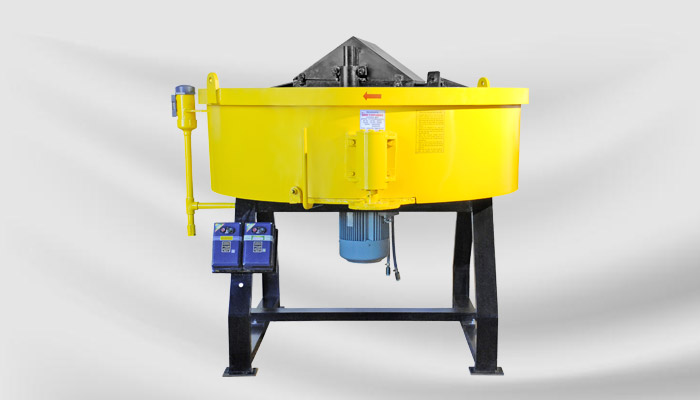
A Concrete Pan Type Mixer is a type of mixer widely used in the construction industry for producing various types of concrete. Unlike traditional drum mixers, the pan mixer has a stationary drum or pan with rotating mixing blades. These mixers are particularly suited for producing smaller batches of concrete with a high degree of homogeneity. They are commonly used for precast concrete production, laboratory testing, and mixing specialized concrete formulations due to their precise and efficient mixing capabilities.
In a pan mixer, the mixing blades rotate inside a fixed, cylindrical pan, ensuring uniform distribution of materials. The materials—cement, aggregates, and water—are loaded into the pan, where the rotating blades mix them thoroughly. The stationary pan combined with the dynamic movement of the blades results in efficient mixing, where the entire batch is exposed to consistent agitation. This system is ideal for evenly mixing stiff and semi-dry mixes, which are difficult to blend in other mixer types.
Standard Pan Mixers Ideal for mixing regular concrete formulations in small to medium batches for general construction purposes.
High-Capacity Pan Mixers These mixers are designed for higher throughput, used in larger precast concrete plants where consistent, high-quality mixing is required.
Laboratory Pan Mixers Smaller, more precise versions of the pan mixer used for research and development in testing facilities to develop new concrete formulations.